
Preheater and Calciner
RCL has five stages of high-efficiency, low-pressure preheating. RCL’s preheater cyclone tower is 108 meters tall. Raw meal is fed from the top of the tower, and it travels from there to the bottom through several cyclones. Each cyclone in the preheater serves as a heat exchanger and a separator. Heat generated and released by the hot gases in our kiln is used in the preheaters to promote energy efficiency. The kiln heat comes in contact with the raw meal in the preheater cyclones as it travels along with the hot gases co-currently in the gas duct of the cyclone. When the raw meal enters the cyclone, it swirls around vigorously and hits the cylindrical walls of the cyclone,losing its velocity. The material drops into the conical cyclone’s bottom and hot air escapes through the immersion tube.
From the top stage of the cyclone tower, material drops stage by stage to reach the cyclone’s bottom stage. Fourth stage cyclone material is diverted into the ILC. As much as 95% of the limestone calcination process takes place in the ILC, at a temperature of 900° C. As a fuel, 60% pulverized coal is fired into the calciner. Coal feed is controlled by a PLC to maintain steady and efficient temperature. Calcination is controlled by particle size, temperature, retention time and partial pressure of CO2 inside the ILC. Calcined material then reaches the rotary kiln inlet for further burning.
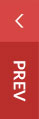
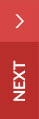