Raw Material Grinding
Next, a measured quantity of limestone is extracted from our limestone hopper. Additives, such as laterite, iron ore or clay, are also extracted from their respective hoppers and mixed with the crushed limestone. These additives are added to the limestone to enhance the reactivity of the limestone during pyro-processing.
All of these raw materials are then ground together in RCL’s vertical roller mill (VRM) in between rollers and table with 100 bar hydraulic pressure. We employ a state-of-the-art model VRM, the ATOX- 47.5, which is supplied by F.L. Smidth of Denmark, which is fitted with a high-efficiency dynamic separator. This is a closed-circuit mill with a recirculation elevator to ensure all the limestone particles are properly ground to required fineness of 90 mic size. When compared to the ball mill grinding technology alternative used by some other cement manufacturers, a VRM is more energy-efficient, reducing our electrical consumption and corresponding impact on the environment. Our VRM can grind even the hardest limestone into fine powder with less energy.
Our ground material’s particle size distribution is an added advantage in pyro-processing. The smaller the particle size, the faster the heat exchange and chemical reaction in the production process. This grants us additional energy and cost efficiency and savings in our production process, thanks to our VRM, all with less impact on the environment. Because of this fine particle size, our limestone gets homogenized in our blending silo and can then be more quickly and energy-efficiently calcined in our preheater. Raw meal samples are taken every hour to check the chemical composition in our XRF and to check the fineness in our particle size analyzer.
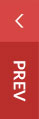
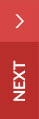